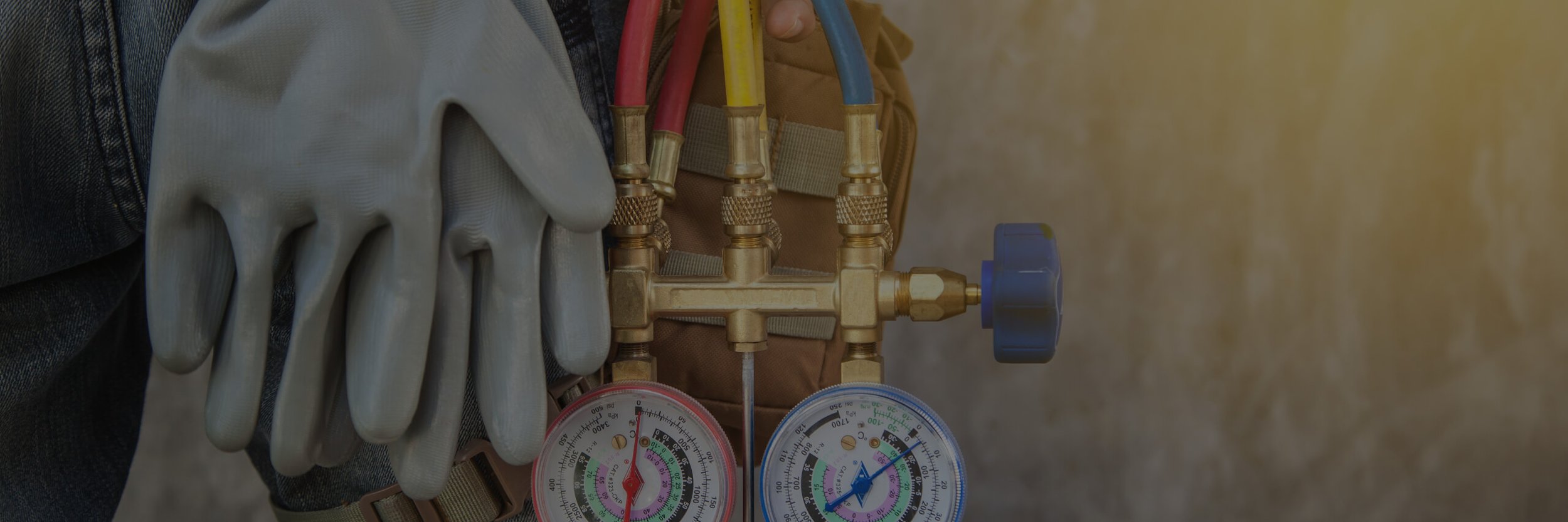
Brazed vs. Flared Linesets: A Comprehensive Guide for New HVAC Technicians
HVACR Licensing & Continuing Education
Brazed vs. Flared Linesets: A Comprehensive Guide for New HVAC Technicians
by Jonathan Kilburn
For HVAC technicians, lineset connections are the backbone of any system, facilitating the flow of refrigerant between components. The choice between brazed linesets and flared linesets is critical, as each method offers unique advantages and is suited to specific applications. Understanding when and why to use each, as well as their respective benefits and drawbacks, is essential for delivering reliable installations. Let’s dive into the applications, pros, cons, and required tools for both methods, concluding with a recommendation for new technicians entering the HVAC field.
What Are Brazed Linesets?
Brazing is a process where copper tubing is joined using a filler metal melted with high heat. This technique creates a permanent and durable bond, making it a go-to method for applications demanding strength and long-term reliability in air conditioning and heat pump systems. This is different that soldering, which is joining two pieces of metal or copper pipe with a softer filler material. Brazing is closer to welding when applied to copper lines.
Brazed linesets are best suited for refrigerant lines used in high-pressure systems where strong, leak-proof connections from the condenser to the evaporator are critical. They are also ideal for installations requiring long-term performance, as the durable bond resists wear and tear over time. In environments prone to vibration, such as those involving large commercial equipment, brazed connections maintain their integrity better than alternatives. Brazing is a versatile solution for custom or retrofit installations, allowing technicians or HVACR contractors to adapt the tubing to fit complex setups with non-standard dimensions or angles by purchasing a line copper tube and cutting it to required lengths.
The primary advantage of brazed connections is their unmatched strength and durability. Properly executed brazed joints can withstand high pressures and is highly resistant to leaks, ensuring optimal system efficiency. This reliability is crucial for meeting the rigorous demands of traditional residential and commercial HVAC systems. Additionally, brazing accommodates various angles and lengths, making it a flexible choice for custom applications. It is widely regarded as an industry standard, especially for larger and more complex systems.
However, brazing comes with its challenges. It requires skill and precision, as improperly brazed joints can weaken over time and become prone to leaks. The process is time-consuming, involving meticulous preparation, heating, and finishing of the joints. Safety is another concern, as brazing involves open flames and high temperatures, requiring specialized equipment and protective gear. Without nitrogen purging during brazing, oxidation can form inside the tubing, potentially causing long-term system damage.
Brazing demands a range of specialized tools, including an oxygen-acetylene torch to generate the high heat needed for melting filler metals, and filler rods made from silver or copper-phosphorus alloys. A nitrogen purging kit is essential to prevent oxidation within the tubing. Flowing nitrogen protects the metal by displacing and removing the oxygen that can cause oxidation of the brazing rod materials on contact. Other tools like a pipe cutter and flux or heat barrier gel are also required to prepare and protect the workpiece. Protective equipment such as gloves, goggles, and flame-resistant clothing is necessary to ensure technician safety.
Once completed, pressure testing the system and drawing down to 500 microns with a vacuum pump ensures a solid connection between the indoor unit and outdoor unit. A little bit of a disclaimer: brazing is not a DIY solution for air conditioner install and should be handled by properly trained HVAC techs. They will be ale to ensure proper function of service valves and connectors while quickly troubleshooting potential problems.
What Are Flared Linesets?
Flaring, on the other hand, is a mechanical process where the end of a copper tube is expanded to fit securely with a flare fitting commonly called a flare nut. This method is particularly popular for ductless mini-split systems and applications requiring quick, reusable connections.
Flared linesets are most commonly used in ductless mini-split systems, where their design aligns with manufacturer specifications. They are also ideal for installations where access is straightforward, as the connections can be easily disassembled and reassembled for maintenance or upgrades making it a preferable option for the DIY Homeowner. Flared linesets are especially useful for pre-charged units with proper specs, as they preserve the refrigerant charge during installation, reducing the need for additional handling. While not recommended, some linesets with flared fittings also come precharged with refrigerant necessary for that specific length.
One of the greatest advantages of flared linesets is their simplicity and accessibility. The installation process is faster and less complex than brazing, making it an excellent choice for new technicians. A system will have specific calculations for the amount of lineset needed for the refrigerant charge. Individuals can purchase the necessary lengths and roll up the excess or cut to length and redo the flare. Unlike brazing, flaring does not require open flames or high heat, reducing fire risks and eliminating the need for torches. Flared fittings are reusable, allowing technicians to make adjustments or repairs without replacing components, and the tools required are generally less expensive, making this method a cost-effective option.
Despite these benefits, flared connections have limitations. They are more prone to leaks than brazed joints, especially if not properly tightened or if the flare itself is imperfect. High-vibration environments can cause flared connections to loosen over time, leading to performance issues. Additionally, while flaring is suitable for ductless mini-splits and smaller systems, it may not be appropriate for high-pressure or large-scale applications. Precision is key when flaring, as the tubing must be cut cleanly and aligned perfectly to ensure a secure seal. If that’s not a possibility the only option is to braze copper linesets.
Flaring requires a straightforward set of tools, including a flaring tool to shape the tubing end and a tubing cutter to achieve clean, square cuts. A deburring tool is used to remove sharp edges inside the tubing, ensuring a smooth and even flare. Proper tightening is critical, and a torque wrench helps achieve the correct tension without over-compressing the connection. For stability during the flaring process, a pipe clamp or vise is also necessary.
Brazed vs. Flared: A Comparison
When comparing brazed and flared linesets, several factors come into play. Brazed connections offer superior strength and leak resistance, making them suitable for high-pressure systems and applications requiring long-term reliability. However, they demand more skill, time, safety precautions, and may void warranties if done improperly. Flared connections, while not as robust, are faster to install and easier for new technicians to learn or DIYer to install. They shine in applications like ductless mini-splits and pre-charged systems, where their simplicity and reusability are significant advantages.
Which Method is Best for Today’s HVAC Technician?
Both brazed and flared linesets have their place in the HVAC industry, and the right choice depends on the system requirements and the technician’s level of experience. For new technicians, flared connections are an excellent starting point. Their ease of installation, minimal tool requirements, and alignment with the growing popularity of ductless mini-split systems make them a practical choice for beginners. The absence of open flames also reduces safety risks, creating a less intimidating learning curve.
As technicians gain experience, learning to braze becomes essential for career growth. Brazing remains the industry standard for traditional HVAC systems, particularly in high-pressure or vibration-prone environments. Mastery of brazing techniques ensures that technicians are prepared for complex installations and can deliver long-term reliability for their clients.
Ultimately, the most successful HVAC technicians will be proficient in both methods. Starting with flared connections allows for quick integration into the field, while developing brazing skills opens doors to more advanced projects and opportunities. By understanding the strengths and limitations of each technique, technicians can make informed decisions that enhance system performance and client satisfaction.